6 Technologies that Elevate Your Machine Tool to Maximum Productivity
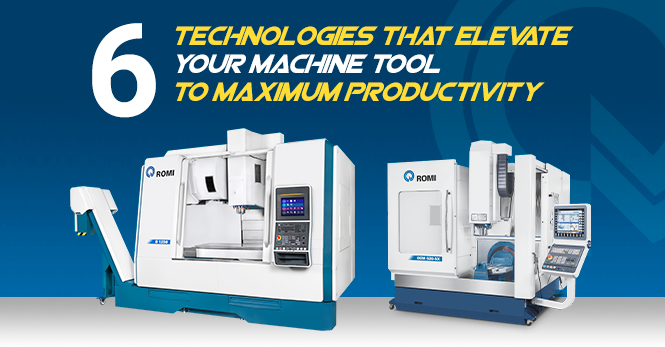
In recent decades, the emergence of new technologies has caused a real revolution in the development of machine tool projects. Machine tools were once limited to being a purely mechanical solutions for chip removal. The addition of digital controls and components with sophisticated and embedded technology, allowed them to today become a part of intelligent manufacturing cells, communicating with other peripherals, such as automatic parts loading and unloading systems, and becoming true operations centers.
From the design of a robust structure to the implementation of electronic components, there is much more than we imagine when it comes to designing and manufacturing machine tools capable of operating more efficiently, while maintaining their accuracy. Below are some of these technologies and components, and an explanation of how they influence the operation of a machining center, allowing for agile and efficient operation:
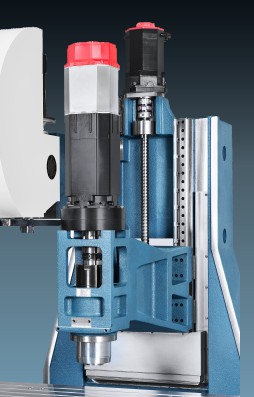
1. Spindle Direct Drive
Considered one of the most important components of a CNC Machining Center, the spindle is the interface between the tool, which removes the material, roughing or finishing parts, and the main motor of the machine.
Spindle Direct Drive – with the motor directly attached to the spindle, they have high acceleration rates, resulting in shorter cycle times. In addition, they have excellent running accuracy even at high speeds. The Spindle Direct Drive, which is featured on the Romi D Series – New Generation machining centers, provides excellent finishing, great transmission efficiency, torque, power, and rotation in versions up to 15,000 rpm.
2. CNC
Dating back to the 1960’s, computers were introduced into machine tool design, a fact that allowed the development of modern equipment. The advent of the CNC made the machines able to repeat with greater precision a sequence of movements, which increased the quality of products produced, reduced rework and waste, and made production lines faster and more flexible.
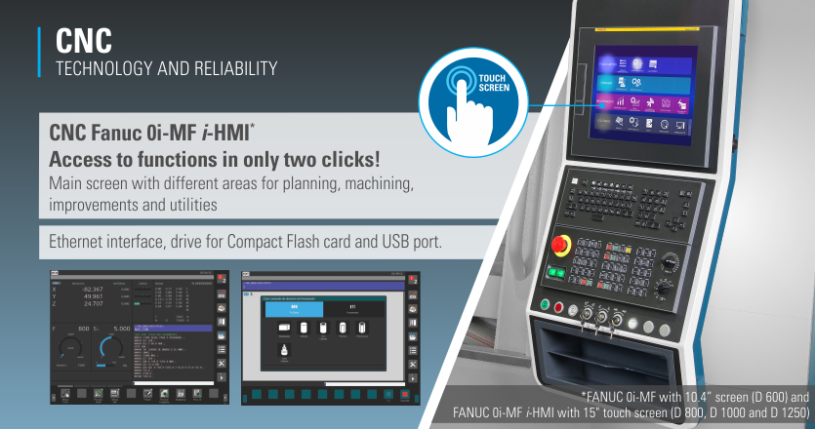
Thanks to the high capacity of processors and the evolution of code and machine language, today’s CNCs process programs much faster. Following advances in the field of information technology (IT), the need for connectivity and the trend towards increasing interactivity with the user, new features have also emerged to facilitate operation and provide an increasingly user-friendly operator-machine experience.
The Fanuc 0i-MF i-HMI CNC, used on the ROMI D800, ROMI D1000 and ROMI D1250 models with 15″ touchscreen monitors, offer the user great programming facilities. The main screen features different areas for planning, machining, improvements and utilities, an allows access to favorite functions in just two clicks. It has Ethernet interface; a Compact Flash card drive and USB port. Other features include:
- Environment that allows viewing various information on a single screen
- Tool manager with the possibility of inserting the drawings, facilitating their identification during setup
- Resources for corrective and preventive maintenance
- Machining programs that can be easily accessed and organized into folders, with visualization of the drawing of the parts
- Visualization of files in various formats
- Multiple interactive machining cycles
3. Linear Roller Guides
Linear guides are elements that allow one component to slide along another, allowing movement within a precise linear pattern, with vibration absorption and high feed rates. Fundamental elements in machine tools, they must be rigid enough not to affect the geometric or dimensional accuracy of the equipment.
Linear roller guides offer high rigidity and less deformation under repeated (varied) floating loads, as the rollers are positioned in a balanced shape, allowing them to receive loads in all directions. Other benefits include:
- Improvement in cutting capacity and better finishing performance
- Extended service life, and smooth, quiet movements
- Low consumption of lubricating oil
- Larger contact area compared to ball guides, obtaining greater load capacity
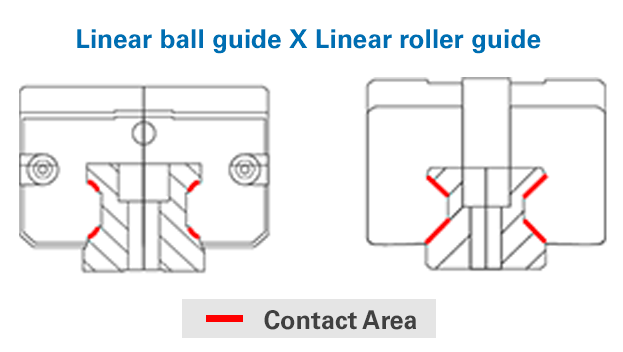
On the ROMI D Series – New Generation – and the ROMI DCM 620 Series, linear roller guides allow high advance and acceleration rates in addition to fast axis positioning. This minimizes passive times and increases productivity.
4. Thermal Compensation System
Thermal stability is one of the fundamental requirements in the design of a machine tool. Solutions to avoid deviations caused by thermal variations have become increasingly essential to obtain greater dimensional accuracy in machining processes.
In a Romi thermal compensation system, through the collection of temperature data from sensors positioned in strategic locations, the CNC corrects the actual position of each axis, allowing tool position to follow a more accurate trajectory, while allowing stable dimensional results even in long periods of work.
All ROMI D Series – New Generation and ROMI DCM 620 Series models have the thermal compensation system, developed to reduce the effects of temperature oscillation on the dimensionality of machined parts.
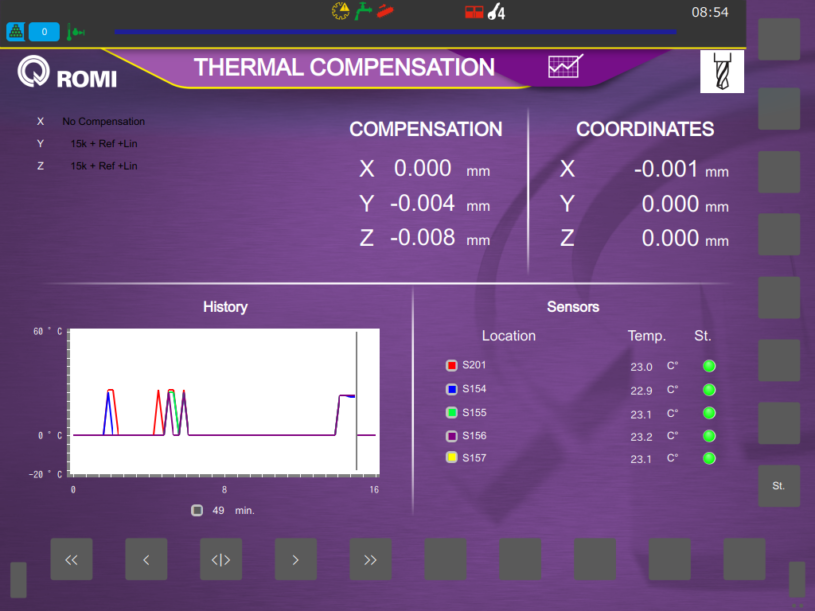
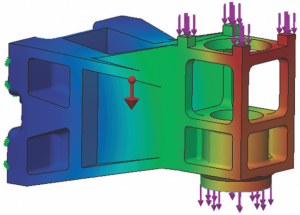
5. Correct component sizing
When we talk about the structure of a machine tool, we can highlight the main component: the base. All other components will be supported on the base and, therefore, it must be able to resist and dampen the effects of vibrations, temperature variations, loads, movements, and other factors. Another structural component is the column, which supported on the base, receives the head/spindle assembly.
Currently we have technologies that simulate real situations of use, allowing design adjustments prior to actual production of a machine tool. Through the use of finite element analysis, for example, it is possible to predict how the structure will behave due to its construction and the arrangement of its components. This makes it possible to evaluate the best configuration with regard to stiffness and deformations. It is important that the virtual modeling of the machine takes into account the actual characteristics such as material, contour conditions and movements, so that the analysis produces reliable results.
The correct dimensioning of each structural component is a determining factor in making a machine tool rigid, and robust. These characteristics allow higher chip start rates, such as those you will see in this ROMI D Series Machining Center video, which is machining at a cutting depth of 14mm.
6. Geometric and performance checks
Before a machine tool is delivered to our customers, we perform checks and tests to assess the performance of the equipment and its suitability with established standards. One of the tests is the Ball Bar, which allows us to check the alignment of the axis and ensure a perfect interpolation of movement.
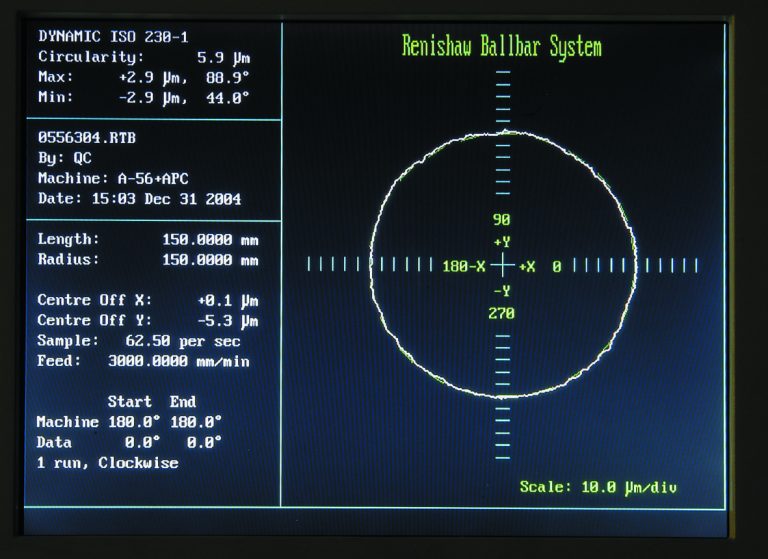
All machines are also inspected with a laser system for positioning and repeatability measurement.
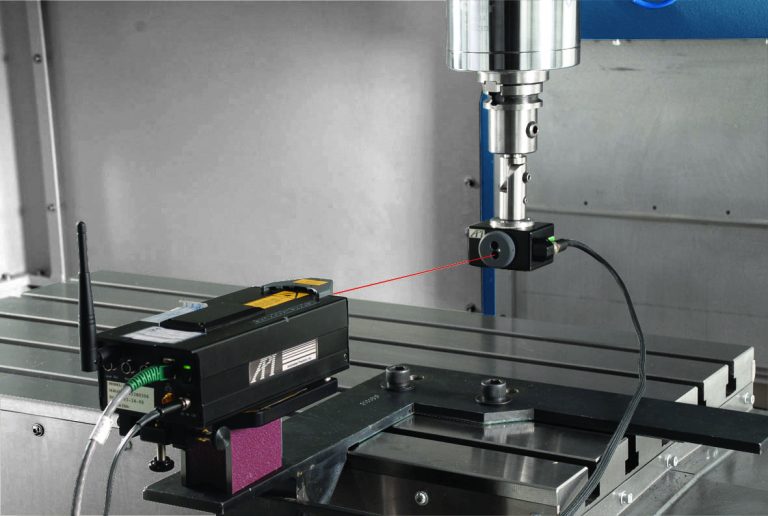
In addition, we perform a 50-hour operating test, in which the equipment is subjected to routines that simulate its use in extreme situations, and allow us to access, for example, the tightness (if there are leaks), its behavior in the movement of the axis and rotations limits, as well as tool changes.