Hybrid manufacturing: Romi introduces a line of machine tools
Additive and subtractive manufacturing in a single machine
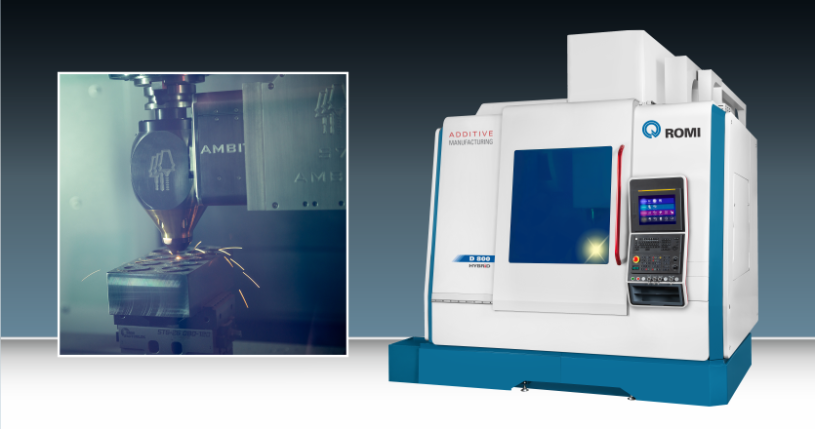
Romi has introduced a complete line of hybrid manufacturing machine tools that combine traditional machining operations with metal additive manufacturing. The new machine is ideal for part repair, adding features, or intricate work where subtractive manufacturing would take more time and produce more waste material.
This new generation of D Series vertical machining centres are the basis for this family of hybrids and include the D 800, the D 1000 and the D 1250. The three models have a robust and heavy casting, roller guides on all axes, big plus direct-drive spindle and a maximum machining volume of 31 x 24 x 25 inches, 40 x 24 x 25 inches and 50 x 24 x 25 inches, respectively. Also available as a hybrid is the Romi DCM 620-5X five axes vertical machining centre.
Romi has made switching back and forth from subtractive machining to additive manufacturing as simple as making a tool change. An automatic tool changer brings the additive head into position, which allows the laser deposition – additive process on the workpiece to begin. The tool changer allows fresh material to be added to the piece in the exact profile, amount and location desired.
Romi teamed with Hybrid Manufacturing Technologies, led by Dr. Jason Jones to make the D Series Hybrids a reality. Hybrid Manufacturing Technologies makes over ten AMBIT FLEX processing heads for the hybrid D series machines. The versatility of these processing heads provides unmatched operational flexibility for a variety of applications, including machining with additive manufacturing (metal, polymer, or composites) and inspection (surface and subsurface). Dr. Jones is the pioneer and world’s leading authority on hybrid manufacturing – integrating Additive Manufacturing (AM) with mainstream CNC machines. He is the co-founder and CEO of Hybrid Manufacturing Technologies.
According to Mr. Rafael Boldorini, General Manager at Romi USA, “While we didn’t invent additive manufacturing, we have made it more accessible for smaller shops with our standard line of Hybrid CNCs. Previously, customers had to spend well over $1,000,000.00 to take advantage of these capabilities. By building our D Series specifically for hybrid manufacturing, we can offer an entry-level machine starting at a much more affordable price point. That has opened the door for a lot of shops to take advantage of this powerful technology.”
The D-Series are equipped with thermal compensation monitored with sensors to improve precision. Each model is equipped with a Fanuc 0i-MF i-HMI CNC with a 15-inch touchscreen, and a high-speed and high-quality package that allows better performance during machining.
Designed and built based on extensive customer research, the New Generation Romi D Series vertical machining centers offer users higher productivity, robustness, and precision. Like all Romi machine tools, they are built with Romi made mono-block cast iron beds that absorb vibration and allow consistent precision production of parts.