Romi Hybrid Machining Centers Enable 3D Metal Manufacturing
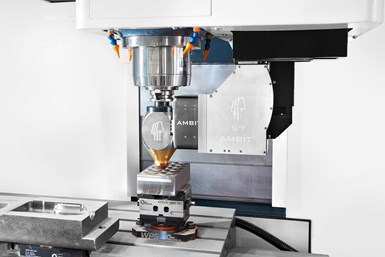
Romi’s line of hybrid manufacturing machining centers combine traditional machining operations with 3D metal additive manufacturing (AM). Its Generation D Series vertical machining centers (VMCs) are the basis for this line of hybrids and include the D 800, the D 1000 and the D 1250. The company says the three models have a robust and heavy casting, roller guides on all axes, a Big Plus direct-drive spindle and a maximum machining volume of 31 × 24 × 25″, 40 × 24 × 25″ and 50 × 24 × 25″, respectively. Also available as a hybrid is the Romi DCM 620-5X 5-axis VMC.
The hybrid manufacturing machining centers are designed to seamlessly switch between subtractive and AM with the switch as simple as making a tool change, the company says. The additive head is brought into position via an automatic tool changer, and the laser deposition/additive process on the workpiece can begin. Material can then be added to the piece in the exact profile, amount and desired location. It is well suited for part repair, adding features or intricate work where subtractive manufacturing would take more time and produce more waste material.
Romi teamed with Hybrid Manufacturing Technologies to create the D Series Hybrids. Hybrid Manufacturing Technologies makes over 10 ambit Flex processing heads for the hybrid D series machines. This enables operational flexibility for a variety of applications, including machining with AM (metal, polymer or composites) and inspection (surface and subsurface).
Each model in the D-Series is equipped with thermal compensation monitored with sensors to improve precision. Each model is also equipped with a FANUC 0i-MF i-HMI CNC with 15″ touchscreen, and a high-speed and high-quality package that enables better performance during machining. According to the company, the D Series VMCs offer users higher productivity, robustness and precision.